Lehmofen Geschichte
Die frühen Kelten hatten, neben dem Feldbrand, kuppelförmige Lehmöfen, ähnlich denen der Etrusker. Diese wiederum hatten ihr Wissen von den Völkern des vorderen Orients. Mit den Brennöfen konnten Temperaturen bis zu 1000 °C erreicht und oxidierend wie auch reduzierend gebrannt werden. Viele archäologische Brennofenfunde in Mitteleuropa gibt es freilich nicht. Denn die Witterung ist zu feucht und das Baumaterial zu vergänglich. Siedlungsfunde in der Landschaft ausfindig zu machen ist oft schwer. Ein oder zwei einsame Brennöfen (wegen der Feuergefahr und den giftigen Dämpfen außerhalb erbaut) sind da noch schwerer zu finden.
Kleine Geschichte des Lehm-Töpfer-Ofens
Im vorderen Orient fand man die wohl ältesten Lehm Brennöfen in Susa (West-Iran) und in Siyalk (Zentral-Iran) aus dem 4 Jh. v.Chr.
Der Susa-Ofen ist ein runder Meilerofen mit durchlöcherter Ofenschale (Lochtenne) von 1,76m im Durchmesser und einem Stützpfeiler im Feuerraum. Solche Öfen sind heute noch in Nordafrika in Gebrauch. |
Waren die allerersten Ton-Brennversuche wohl allesamt Grubenbrände (Töpferware und Brennmaterial liegen dicht beieinander), ist hier das Brenngut vom Brennmaterial getrennt. Der Ofen wurde nach oben mit zerbrochenen Scherben abgedeckt, zwischen denen der Rauch abziehen konnte. Auch fanden die Töpfer schnell heraus, dass die Temperaturverteilung verbessert wurde, wenn man nicht nur wenige, sondern zahlreiche kleinere Löcher in der Tenne anlegte.
Eine Wasserschale im hinteren Feuerraum sorgte für einen verbesserten Zug. So riss das aufsteigende, verdunstende Wasser die heißen Ofengase mit sich nach oben.
Die ersten Öfen mit kuppelförmigem Gewölbe wurden im zentraliranischen Siyalk (4.Jh.v.Chr.) gefunden. Hier war die Ofenkonstruktion komplizierter. Die Brenngase wurden, zur Schonung der Malerei, über ein Kanalsystem geleitet. Die Luftzufuhr konnte durch Tonscherben in den Kanälen reguliert werden.
In Siyalk III (3500 v.Chr.) ist ein Ofen ausgegraben worden, der eine Brennkammer von 1,05 x 1,10 x 0,45 m mit drei Frischluftöffnungen und achtzehn Rauchkanälen hat. In ihn wurde die Keramik, anders als im oben beschriebenen Ofen, zusammen mit dem Brennstoff gelegt und schwarz bemalte Ware auf roten Grund gebrannt.
In Griechenland tauchte später eine vereinfachte Form des kuppelförmigen Gewölbes, mit großem Feuerraum unter der Ofensohle auf. Sie verfeinerten die Technik und legten einen überdachten ca. 60 cm tiefen Vorherd (Brennkanal) an, für langflammige Holzscheite. Auch die Etrusker übernahmen diesen Kuppelofen, der heute als korinthischer Ofen mit aufsteigender Flamme bezeichnet wird.
Im runden Brennraum liegt auf einem Stützpfeiler eine dicke, mit vielen Löchern versehene Schamottplatte (die Lochtenne). Darüber ist mit gebrannten Tonziegeln und Lehm ein nach oben offenes Gewölbe gemauert.
|
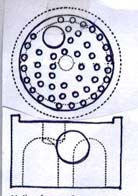
|
Die Öffnung wird, wenn der Ofen befüllt ist, mit zerbrochenen Scherben so abgedeckt, dass der Rauch noch abziehen kann. Mit solchen Öfen kann man oxidierend wie auch reduzierend brennen.
Beim oxidierenden Brand lässt man den Ofen nach dem ca. achtstündigen Brand mindestens einen Tag abkühlen, bevor man die Keramik entnimmt. Vorher roter Ton ist rot, weißer ist weiß geblieben.
Beim reduzierenden Brand erzeugt man am Ende des Brennvorganges eine sauerstoffarme Ofeninnenatmosphäre, indem man die Sauerstoffzufuhr von außen stoppt. In das Innere des Ofens kommt vor dem Abdichten viel organisch-trockenes, leicht entflammbares Material (Zweige, Stroh …). Haben die trockenen Halme Feuer gefasst, wird zuerst der Brennkanal (Eisenplatte) und danach die Kuppel (auf die Scherben Lehm gießen) des Ofens fest verschlossen und mit Lehm jede Ritze verschmiert, so das keinerlei neuer Sauerstoff in den Ofen gelangen kann. Das Feuer der Zweige stillt jetzt seinen Hunger nach Sauerstoff, indem es zuerst die freien Atome „schluckt“. Ist in der Luft nichts mehr zu finden, zieht es sich den Sauerstoff aus den Keramikscherben heraus – der Ton verfärbt sich schwarz. Vorher roter Ton ist nun schwarz, weißer auch. Die Ware ist reduzierend gebrannt. Beim Reduktionsbrand ist es besonders schön, wenn die Keramik vorher poliert wurde oder wenn man direkt neben die polierte Keramik getrocknete Pflanzen oder Quarzsand gibt. Glanzstoffe können so an den Scherben abgegeben werden.
Interessant ist, dass man diese Schwarzfärbung rückgängig machen kann, indem man die schwarzen Stücke nochmals oxidierend (mit Sauerstoff) auf 600-700 °C erhitzt. Der Scherben nimmt sich jetzt wieder den gestohlenen Sauerstoff zurück und seine ursprüngliche Farbe kommt wieder zum Vorschein.
Weitere kuppelförmige Brennöfen mit Lochtenne findet man seit dem 4 Jh.v.Chr. im ganzen fruchtbaren Halbmond.
In Habuba Kabira, am Euphrat zeigt eine weitere Variante einen Ofentyp, der einen seitlichen Schacht zur Beschickung der tiefer gelegenen Feuerkammer aufweist. Die kuppelförmige Abdeckung aus Lehm und Reisig wurde jedes Mal nach dem Einsetzen der Keramik neu errichtet und zur Entnahme wieder abgerissen.
Solch ein Ofentyp wurde aus der späten Urnenfelderzeit (870-820 v.Chr.) im Landkreis Neu-Ulm gefunden. |
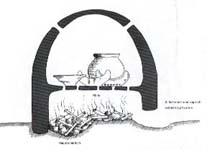 |
Lehmofenbau
Mittlerweile war ich bei zwei Lehmofen – Aufbauten und etlichen Bränden mit dabei und möchte hier die gesammelten Erfahrungen (die mir, verglichen zu dem riesigen Themengebiet, recht klein vorkommen) weitergeben.
Das Schöne daran ist, dass ein Lehmofenbrand etwas sehr Lebendiges ist. Nicht zu vergleichen mit der Exaktheit des Elektroofens, bei dem man die Brennkurve einstellt, Start drückt und schlafen gehen kann.
Durch das Anfeuern des Holzes im Brennkanal, das ständige, gleichmäßige Nachschieben der Glut in die Brennkammer, die halbstündige Kontrolle der Ofeninnentemperatur, ist es ein Aufwendiges aber auch zeitintensives erleben des Brandes. Und nicht zuletzt hat man viel, viel Muße den Flammen des Feuers zuzuschauen – schön!
Außer gebrannten Tonziegeln zum Mauern benötigt man eine feuerfeste Unterlage, den richtigen Standort (einfallende Winde in den Brennkanal können zu unangenehmen Temperaturschwankungen führen – bei fallendem Luftdruck zieht der Ofen schlecht), viel gemagerten Lehm (als Mörtel- und Verputzmasse), einen langen Eisenschieber (zum Zurückschieben der Glut), feuerfeste Handschuhe, Schamottplatten oder Eisenstangen (um die Keramik über der Glut zu platzieren), einen Temperaturfühler, evtl. ein Ofenrohr (falls der Ofen alleine nicht „ziehen“ will) und Platten zum Abdichten des Ofens, falls man reduzieren möchte.
Die Wände des Lehmofens sind später wasserempfindlich. Es empfiehlt sich daher, den Ofen zu überdachen (Vorsicht! Darüber wird es sehr heiß bzw. die Brenngase sind giftig). Es gibt auch die Variante, um den gemauerten Ofen nochmals eine Lage Steine zu schichten und die entstehenden Lücken mit frischem Lehm auszugießen. Die Steine werden so gelegt, dass eventueller Regen abfließen kann. Aber ich denke ein hohes Dach ist einfach am Sichersten. Die ersten Lehmöfen wurden aus luftgetrocknetem Lehm gemauert und hatten kein Ofenrohr. Der Rauch zog durch eine lose darüber gelegte Scherbenschicht. Plant man eines mit ein, muss man sich nur Gedanken über deren Befestigung machen, denn das Rohr wird natürlich sehr heiß.
Zuerst muss der gestochene Lehm durch Schlämmen und Magern vorbereitet werden.
|
Das Schlämmen mit Wasser macht ihn geschmeidig, das Magern soll das Reißen des Lehms reduzieren, wenn er sich durch die Ofenhitze verfestigt. Als Magerungsmittel eignen sich Sand, Sägespäne Stroh oder Mist. Wenn das Ganze auf eine dicke Plastikplane ausgebreitet wird und mehrere Personen kräftig mit den Füßen darauf herum stampfen, wird es schnell eine homogene Masse. Sie ist fertig, wenn Lehm, Wasser und Magermittel einen schweren, zähen Matsch ergeben (ähnlich dem Putzmörtel). |

|
Auf die feuerfeste Unterlage (gemauerte Tonziegel, Zementgrund) wird nun die Grundform des Ofens mit Tonziegeln gemauert. Als Mörtel nimmt man den Lehm. Die Tonziegel und den Untergrund feuchtet man gut an, damit der Lehmmörtel sich gut damit verbindet. Der runde Brennraum (hier ca. 70 cm im Durchmesser) und der 40-50 cm lange Vorherd (in dem das Holz vorgeheizt wird) sind nun gut zu erkennen. Den Vorherd nicht zu lang bauen, sonst kann später die Glut nicht gleichmäßig unter der Keramik verteilt werden. —> |
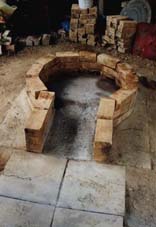 |
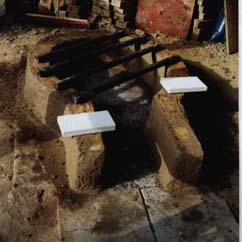 |
<—
Hat man zwei, drei Runden gemauert, muss man sich entscheiden, wie der Brennraum gestaltet werden soll. Gibt es einen einfachen Eisenstangen-Rost oder wird eine Lochtenne mit Schamottstütze eingearbeitet? Massive Eisenstangen haben den Vorteil, dass sie haltbarer als Schamotte sind. Sie verbiegen sich vielleicht mit der Zeit ein wenig. Ein Nachteil sind die großen Zwischenräume. Die Keramik ist so ungleichmäßigen Temperaturschwankungen direkt ausgesetzt (bei ungleichmäßiger Verteilung der Glut), es kommt leichter zu Rissen. Die Lochtenne (Schamottplatte mit Löchern) mit Stützpfeiler hat den Vorteil, dass die heißen Gase gleichmäßiger verteilt um die Keramik strömen können. Die Wärmeverteilung im Ofeninnenraum ist optimaler.
Ein Nachteil ist die relative Zerbrechlichkeit von Schamott. Eine Lochtenne geht schneller kaputt. Auch muss die Glut um den Stützpfeiler herumverteilt werden, was eine gewisse Übung erfordert. |
Hier hat man sich für massive Eisenstangen (zugegeben sehr dick) entschieden. Man sieht deutlich die großen Zwischenräume. –> |
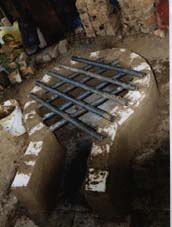 |
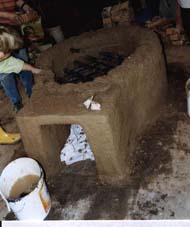 |
<–
Es wird weiter hochgemauert und, will man einen Temperaturfühler die Ofeninnentemperatur messen lassen, eine Aussparung in der Ofenwand freigelassen. Einfach einen Stock mit einbauen, der später wieder herausgezogen wird. Einen Überblick über das Ansteigen der Temperatur zu haben ist ratsam. Schneller als 150°C pro Stunde sollte sie nicht steigen, sonst reißt der Scherben. Die Vordecke wird entweder als Rundgewölbe gemauert (schwierig) oder es werden vorher angefertigte Schamottplatten auf die Ziegel gelegt (einfach). Wichtig: man sollte von der Feuerstelle nicht in den Brennraum schauen können!! Die heißen Gase sollen ja von unten aus die Keramik erwärmen und nicht sofort an der Ofenwand entlang zum Schornstein hinaus ziehen. Energieverlust. Das war hier nicht optimal geregelt worden… |
Nun kann der Ofenraum nach, oben verjüngt, hochgemauert werden. Wichtig ist, immer ein, zwei Zentimeter Lehmmörtel zwischen den Tonziegeln zu lassen, dass die Hitzeausdehnung nicht zu Sprüngen führt. Der Ofen wird innen wie außen verputzt. Hat er eine Höhe von 130 bis 140 cm erreicht, sollte man ihn so belassen, da sonst das Befüllen von oben (er ist sozusagen ein Toplader) zu schwierig wird. Der Ofen kann jetzt durchtrocknen oder man entfacht ein Trocknungsfeuer. —> |
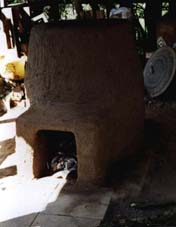 |
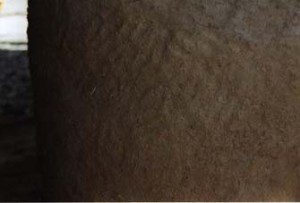 |
Hier nochmal zum Vergleich:<—
Erst die Ofenwand mit frisch verstrichenem Lehm, gerade hochgemauert und mit den Händen festgeklopft. |
Hier dieselbe Stelle nach dem ersten Brand. Es sind deutliche Risse erkennbar, die vor jedem weiteren Brand ausgebessert werden müssen. Einen Lehmofen muss man pflegen. —> |
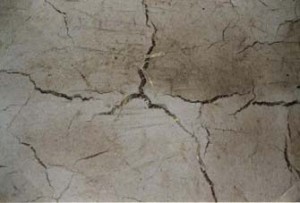 |
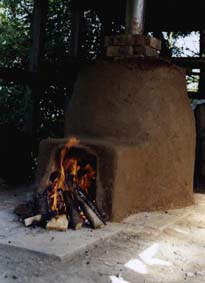 |
<—
Steht der Ofen günstig, so wird nicht unbedingt ein Ofenrohr benötigt. Die Hitze findet schon ihren Weg durch die Brennkammer nach draußen. Es kann aber natürlich einer eingebaut werden. Hier wurden Eisenplatten so auf die Öffnung gelegt, dass ein Spalt für das Rohr frei blieb. Dies wurde darauf gestellt, mit weiteren Ziegeln stabilisiert und alles mit Lehm gut abgedichtet. Einen weiteren Halt findet das Rohr beim Austritt durch das hier gezimmerte Dach. |
Geheizt wird wie folgt: Ganz vorne liegen Holzscheite zum Anwärmen, in der Mitte sind diejenigen, die gerade brennen und ganz hinten befindet sich nur die reine Glut. Sind die mittleren Scheite gut durchgebrannt, werden diese als neue Glut nach hinten geschoben, die getrockneten rücken vor und dürfen jetzt brennen, es werden frische, zum anwärmen dazugelegt. Es ist ratsam zwischen den Holzscheiten immer genügend Platz für die Luftzufuhr zu lassen. Dann läuft alles besser. —> |
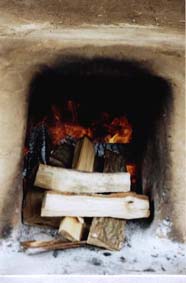 |
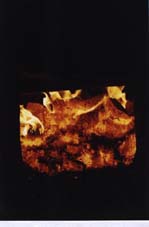 |
<—
Die Endtemperatur ist erreicht (es ist mittlerweile Abend) und die restliche Glut wurde unter die Keramik geschoben. Jetzt muss der Ofen langsam abkühlen (Oxidationsbrand) oder das organische Material eingebracht und der Ofen verschlossen werden (Reduktionsbrand). |
Hier die selbe Einstellung am Morgen danach. Im Vorherd ist keine Asche mehr. Sie wurde ja vollständig in den Brennraum geschoben. —> |
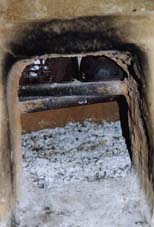 |
Blick in den Ofen nach der Abkühlphase, nach dem der Schornstein mit den Eisenplatten abgenommen wurde.
—>
Das Reduktionsmaterial, was in diesem Fall vor dem Schließen des Ofens oben in den Innenraum hineingeschüttet wurde, ist verbrannt und liegt als Asche auf der Keramik. |
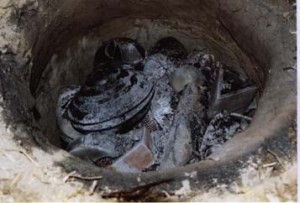 |
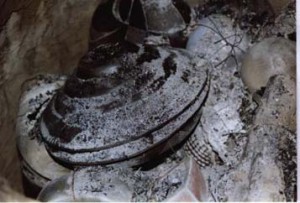 |
<—
Zwei getreppte, polierte Schalen sind umgedreht auf ein Kegelhalsgefäß gelegt worden. |
Das gewaschene Ergebnis.
—>
Wo das Feuer keine Kraft mehr hatte den Ton zu schwärzen und Sauerstoff übrig blieb, hat der lederfarbene Ton seine Farbe erhalten können. Es entstanden sehr schöne Farbverläufe. |
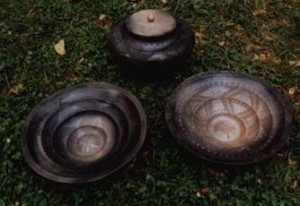 |
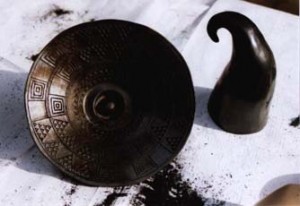 |
Sehr schön ist auch polierter Graphit.
<—
Graphitschale und poliertes Horn kurz nach dem Öffnen des Ofens mit Aschespuren. |
Hier kann ich noch einmal gut zeigen, wie der Reduktionsbrand eine Keramik verändern kann.
—>
Vor dem Brand sieht man schön den Farbkontrast von lederfarbenem Ton zu den schwarz polierten Graphitflächen. |
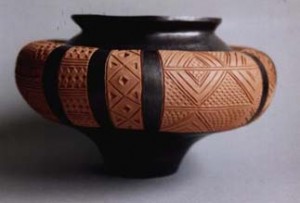 |
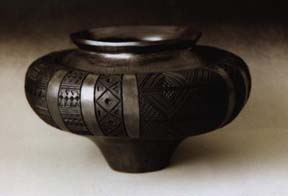 |
<—
Nach dem Schwarzbrand strahlt der Graphit. Der lederfarbene Ton ist nunmehr ganz schwarz geworden. Solche Gefäße sind allerdings, weil nicht glasiert, nicht dicht. |